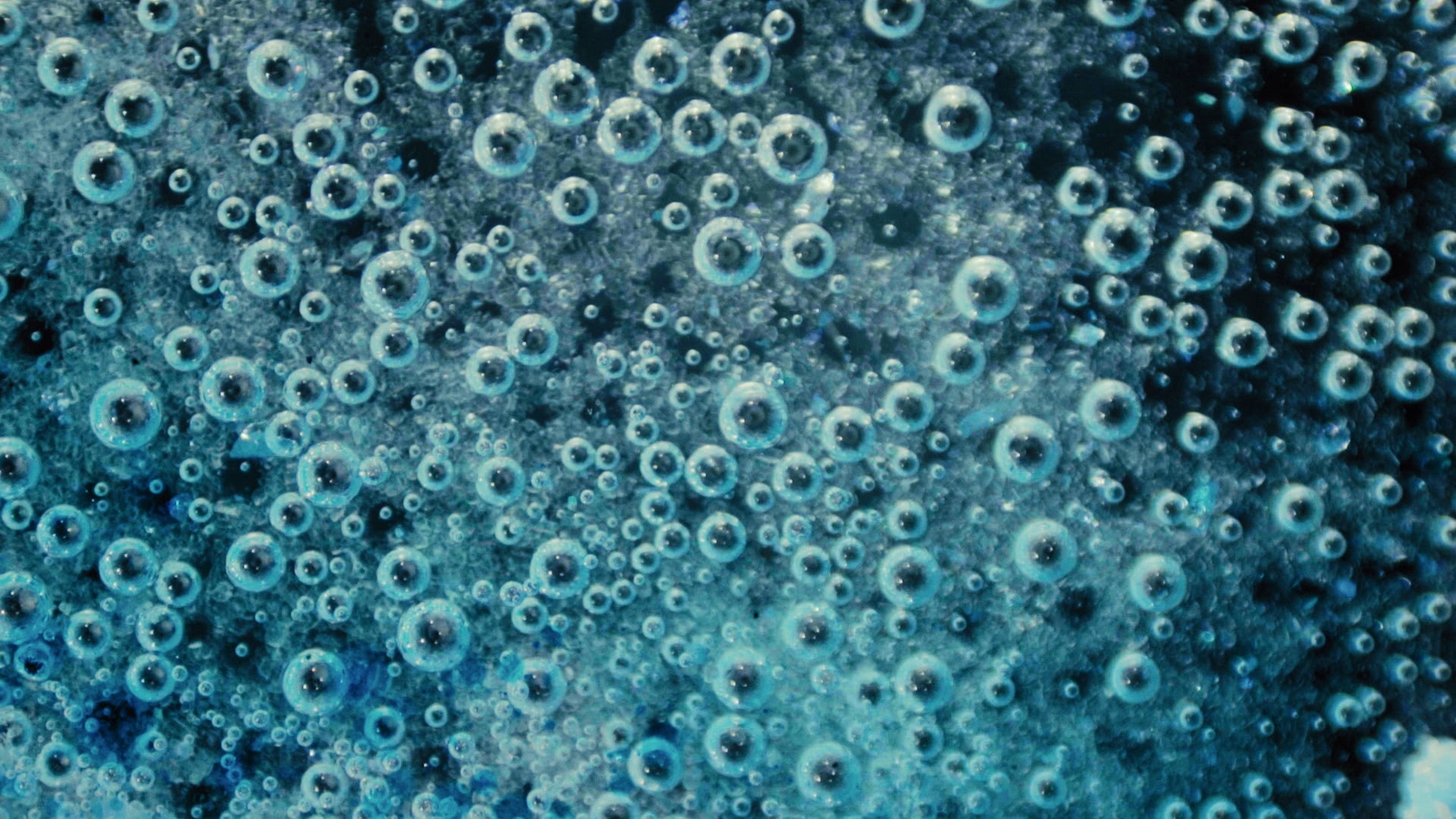
24 Jun Permanently Preventing Paint Failures
The problem lies in the sequence.
Large petrochemical, food-processing, paper mills and many other firms and large commercial facilities are waiting for Covid-19 to play out. In many cases MRO (maintenance, repair and operations) practices are, likewise, on hold.
I know this for a fact after speaking with some or our larger clients.
Yet if you’re planning any paint, coating or other MRO work, the time to act is now.
Why? I’m glad you asked!
Because paint and coating failures are always sequential and very nearly always preventable. And the best way to mitigate a failure is to identify the first possible moment to disrupt the sequence. This is true for aviation disasters, the Titanic, and peeling paint.
It starts long before the contractor is selected, the specification is written, the PO’s are cut or even a material selected. It begins with the assumption that something requires corrosion mitigation, or other reasons for painting or coating to take place.
The very nexus of the sequence often begins with: “I wonder what paint system we should use here? Let’s call a paint supplier.”
It’s the wrong initial question and certainly the wrong first call. The proper sequence is, “I wonder if this needs to be painted, or are there other ways to solve this problem? Let’s do some research.”
The quote from Albert Einstein comes to mind when asked if he had an hour to save the world: “…I’d spend 55 minutes thinking about the problem and 5 minutes thinking about solutions.”
A quick case in point:
I was asked a few years ago to comment on a coating system that had been specified for lining the interior of a large concrete tank in Europe. The tank could only be taken out of service once every 7 years and the facility could not function without it.
I found the material mediocre, and the specification worse. Had the project moved forward, the system would not have performed as anticipated, and resulted in a failure. POs had been issued but work had not begun.
But I looked deeper and questioned the entire assumption – did the tank need to be coated?
I asked to review the remote RV inspection report, videos and other information. The tank had cracked, and crack injection had been performed from the exterior. The tank stopped leaking, and otherwise was fine. There was nothing in the water that would attack the concrete, and the rebar had been coated and was at a sufficient depth within the concrete to not be bothered by the liquids stored in the tank.
I advised my client not to coat the tank at all.
This 6-hour evaluation saved the client upwards of $1 million. (I never got paid, BTW).
Most importantly, we got in front of the sequence and stopped the process.
I’ve been personally involved in many dozens of paint and coating failures and studied hundreds more. I’ve also studied hundreds of failures in aviation, spaceflight and military actions.
They all have one thing in common: There is a sequence. I’ve been scolded by my social-media guru to keep my blog posts shorter. So I don’t have room to expand on this as much as I would like, but I will challenge you to think of a failure, any failure. And you will find a sequence. And, as you think this through, you’ll find that the earlier you break the sequence, the better.
I’m throwing out a challenge! In the comments section, post any failure you like – and we’ll evaluate the failure for proper sequencing.
Come on. I dare you!
Sorry, the comment form is closed at this time.