20 Dec Corrosion Conundrum Or, “What the heck is that?”
This blog contains two questions. I have the answer to one of the questions but remain mystified by the second. I hope you take the time to respond!
It’s not often that I become flummoxed when getting called out to a corrosion mitigation project. Having worked on the largest radio telescope in the world, specified the coating system for all the drinking water tanks in the tallest building in the world, and having worked on thousands of other projects, this one was a doozy.
It falls into the rarified category I call, “What the heck is that?”
THE CRIME SCENE:
We were called to conduct a condition survey on a bunch of bolted-together (field-erected) silos which contained various dry materials.
The owner, a global powerhouse whose name we must keep confidential, indicated that the silos were between 30 and 60 years old – not that it matters one iota from a corrosion perspective. Steel doesn’t know how old it is, it just knows what condition it’s in. Interestingly, it’s the same for me: I don’t know how old I am because I’m so old, I can’t remember.
Back to our silos.
We identified a veritable smorgasbord of corrosion, including evidence of general pitting, crevice and laminar distress. In explaining the difference to our client, I compared it to a doctor telling me “You could afford to lay off the Oreos chubby boy, but it’s not an urgent matter.” I mentioned to our client that laminar is really serious, with crevice and pitting right up there. In some cases, the steel had perforated.

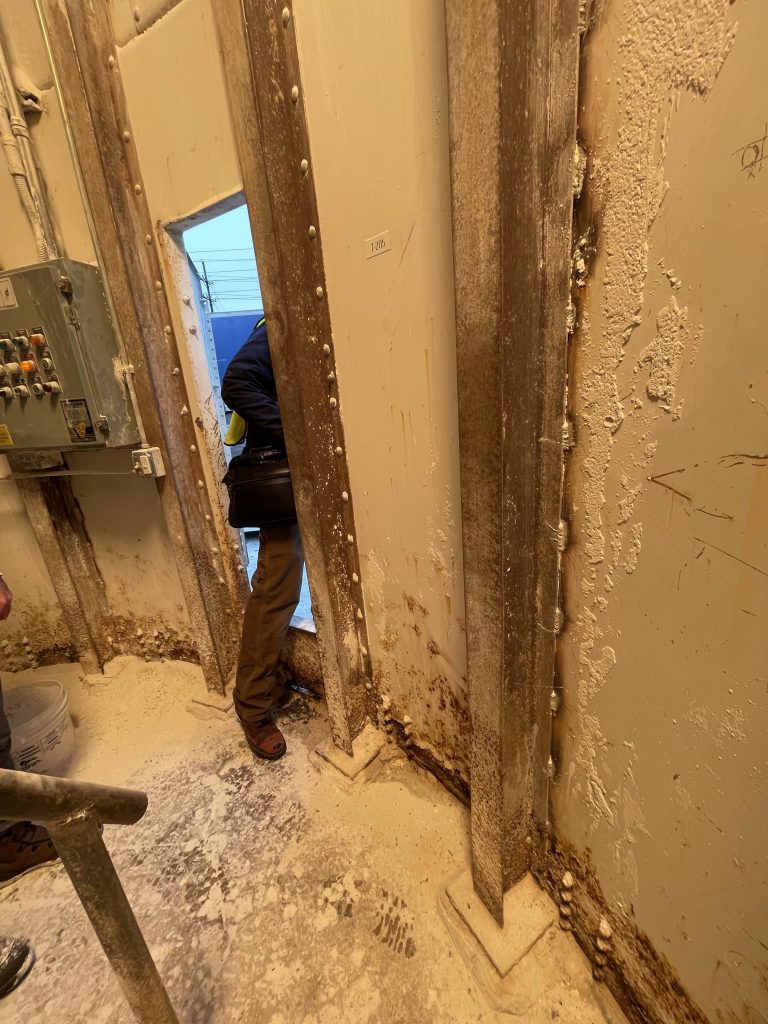
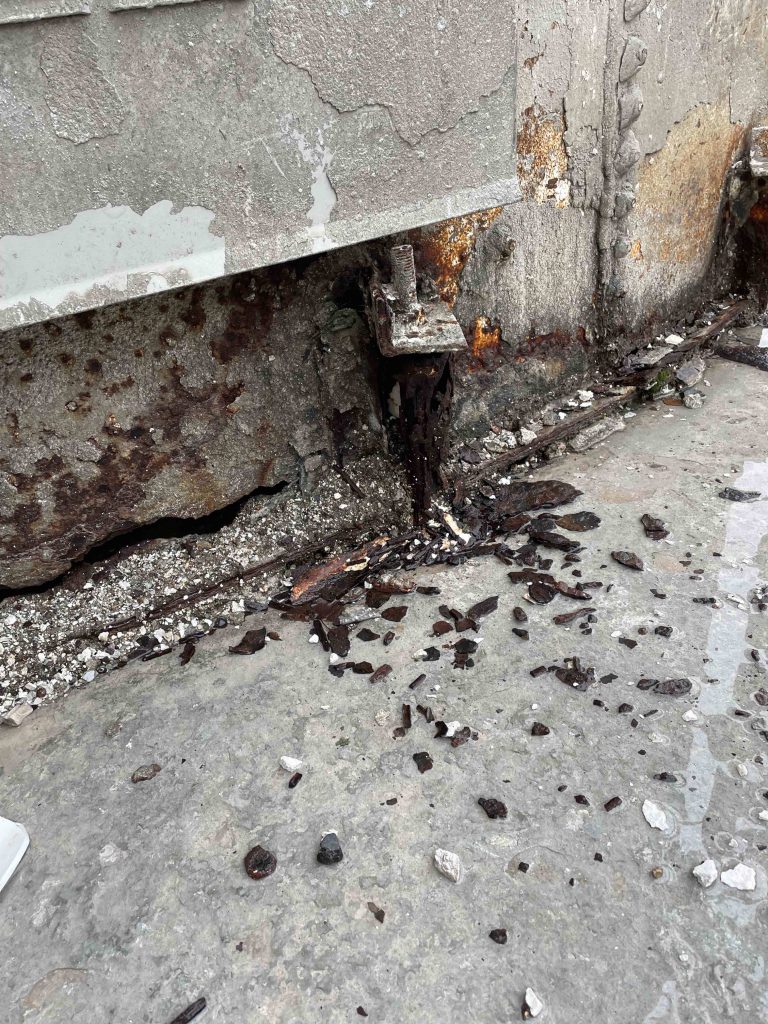
The bulk of the most severe corrosion was near the concrete floor, where the silos rested, and the worst was located beneath the door, on the shell frame.
They couldn’t figure out why the corrosion was so severe on all the silos in the same location.
Question #1 – What do you think caused the severe corrosion that led to perforations beneath each door?
Our proposal to our client will include:
- A condition survey of each silo.
- A remediation plan for each of the various types of corrosion.
They had contacted other firms and, of course, welders wanted to weld, and paint companies wanted to blast and coat everything, as did the coating contractors.
My firm, Chicago Corrosion Group, provides vendor-neutral, client-centric consulting. We recommend the least costly, most technically sound means of remediation, and our specifications will identify one material and surface-prep standard for all those areas exhibiting laminar, crevice and pitting corrosion, and a much less aggressive blast profile and less costly material selection for those areas exhibiting general corrosion.
The result will be a precise solution for our client, along with substantial savings. In fact, we think we can provide them a 20-year, no-maintenance service life for even the most corroded areas.
Question #2 – What the heck is that?

We identified an unusual “bullseye” type of corrosion that I had not seen before. The bullseyes were on the silo exteriors. Initially, I thought that, perhaps, someone had spot-welded on the silo interior, burning the paint on the exterior and leading to the unusual distress pattern, but there was no evidence of this on the interior. For our purposes, I don’t really care what caused the corrosion. Our solution will be the same; wash (to remove any contaminants) blast and touch-up, feathering onto the existing, well-adhered paint system.
But it remains a curiosity.
Eager to hear your thoughts about both questions.
Please leave your comments below.
This technical blog is exclusively for your benefit. Please email me, or post comments, about what you’d like to hear more about. Or send me your challenging corrosion-mitigation and distress stories!
Sorry, the comment form is closed at this time.